長引くコロナ禍、現場の品質はどう担保する!? いすゞテクノ現場の生の声を聞く!「コロナ禍の海外工場の人材育成」セミナーレポート
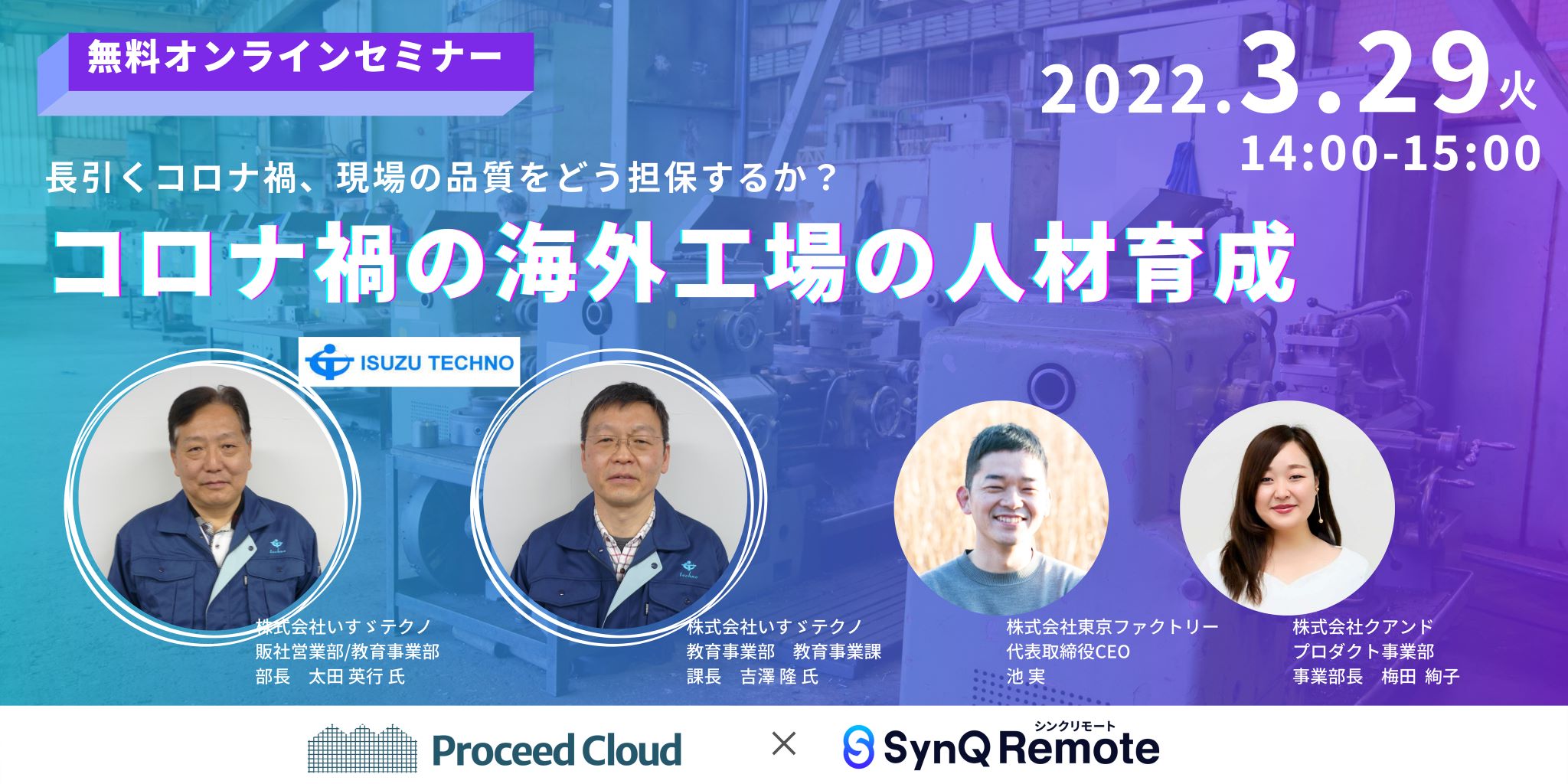
コロナ禍において海外工場へのスーパーバイザーの派遣や出張のハードルが高い状況が続いています。海外工場の人材育成は製造業における大きな課題と言えます。今回のセミナーではいすゞテクノで海外工場の品質管理や教育を担うお二方をお招きして、現場の生の課題や改善の取り組みについてうかがいました。製造情報の見える化と製造情報データベースの構築を実現するクラウドサービス「Proceed Cloud」を提供する東京ファクトリーとともに、コロナ禍の「現場」の未来を模索しました!
いすゞテクノとは
いすゞ自動車株式会社の子会社として、あらゆる製造業における生産ラインの新設やメンテナンス、プラントへのエネルギー供給設備の構築などを行っています。日本3拠点に加え、タイとインドネシアに海外拠点を持ち、技術者集団として国内外のものづくりを支えています。中でも海外の工場において実践教育を担当する教育事業についてお話を伺います。コロナ禍における海外工場の品質管理と教育の課題
梅田
長引くコロナ禍ですが、海外への渡航制限が具体的にどのように業務に影響してきたのか教えてください。
太田様
日本から直接技術者が赴くことができないため、海外工場内でいかに質の高い教育を続けていくのかというところが課題になっています。コロナ初期は、駐在員や以前日本で教育を受けた実習生が先生の代わりとなって教育を実施していました。しかし駐在員はどうしても専門分野に偏りがあったり、人数も限られたりしますし、現地人材は「自分のスキルは自分のスキルアップのためのもの」と考えているため、周囲の人に惜しみなく伝えるということに抵抗があったりする場合もあるようです。
QCストーリーやいすゞのものづくりの考え方が浸透していない
吉澤様
教育に困っているといっても、今一番必要なのはどのような教育内容なのかを把握するため、まずは海外拠点にヒアリングしてみました。すると大きく2つの課題が浮かび上がってきました。
ひとつめは、海外の現場担当者がQCストーリー(製品を製造する過程において不良発生原因の分析や製造工程の見直しなどの検証する手法)を深く理解できていないということです。品質不具合や生産の遅れなど、現場では様々な問題が発生します。それに対して、駐在員が現場担当者にこれって調べた?ここのことって現状把握できている?と聞いていくと、最終的には全く的外れな対策がなされていたということが度々発覚するようなのです。
もちろん現地の担当者も座学でQCストーリーとはこういうものだよ、こういうグラフを使うんだよということは習ったことがあります。ただ実践でその知識をどう活かすのかは分からず、現場に落とし込んだ深い理解ができていなかったのです。これを受けて、まだトライアルの段階ではありますが、2週間に1回、日本と現地をつなぎ、QC実践教育を行うことにしました。日本の教育者から問題を出し、海外の現場担当者に現状把握をさせて、対策を考えさせ、フィードバックをするというものです。
ふたつめは、「いすゞのものづくり」の思想が浸透していないということです。座学で習っても腹落ちしておらず、このものづくりに対する基本的な考え方が行動に反映されていないということでした。中にはトップダウンは通用するが、日本の駐在員の言うことをなかなか理解してもらえないというお国柄もあったりします。そんな中で海外工場に対する教育を一律で行うのではなく、その土地に合わせた教育方法で「いすゞものづくり」の基本を伝えていくことが重要だと痛感しました。
梅田
コロナ禍以前はQCストーリーやいすゞものづくりの考え方についてどのように教育されていたのですか?
吉澤様
コロナ前は日本から講師が出向いて、1~2週間程度短期集中の実践研修を行ったり、現地からリーダークラスを日本に呼び寄せて実際の日本の現場を見せるというようなことをやっていました。どちらにしても三現主義(机上の空論ではなく「現場」で「現物」を見て「現実」を認識すること)を重視して、何が問題なのかを自ら体感させ、考えさせるという教育を行ってきました。
いすゞものづくりは昔から金太郎飴に例えられてきました。どんな現場でも、誰が担当しても同じ品質が再現できる、そのような高い品質は教育によってこそ保たれてきたので、コロナだからとおろそかにすることはできないという危機感がありました。
SynQ Remote(シンクリモート)を使った海外工場の教育
梅田
コロナ禍になったとき、最初はどういう方法で教育を続けようとされたのですか?
吉澤様
最初は、学習塾もリモートができるんだからリモートで現場教育してみるか!ということで、従来から事務所同士の会議で利用していたMicrosoft TeamsやLINEを利用して試験運用をしてみました。しかし、話している対象物が画面上のどれを指しているのかが思った以上に伝わらないのです。「右のその白いの!」「左のその赤いの!」と通訳を介しながらの会話だと、伝えたいことが伝わっているのか全く見当がつかない状態になりました。
そこで、現場に特化したツールを調べていく中でSynQ Remote(シンクリモート)に出会ったんですね。他にもツールは検討しましたが、コストが高いものも多く、SynQ Remote(シンクリモート)の手軽さに惹かれて無償トライアルを始めました。実際に使ってみると、指導者と作業者の双方からポインタを出すことができ、お互いにスムーズな意思疎通が図れました。私が指し示しながら話している部分に対して、相手が「ここのことですか?」という確認もできました。当初は実践だけを想定していましたが、ポインタやお絵描きの機能は座学にも有効でしたし、画像や録画データを復習に使うこともできました。
セキュリティの壁
梅田
ありがとうございます。SynQ Remote(シンクリモート)を使ってリモートでの海外工場の教育をスタートされたわけですが、その中でも現状課題になっていることはありますか?
吉澤様
端末を現場に持ち込むことに関するセキュリティの問題ですね。会社の生産状況や設備の情報、ものづくりの仕組みそのものが写真や動画で保存されることになります。SynQ Remote(シンクリモート)の場合はクラウド上に保存されますが、ここにアクセスできる人を制限する必要があるなど、本社のIT担当からの要求事項が多岐にわたりました。
クアンドさんにも長らく対応をいただいており、多要素認証や権限管理のしくみをこれから開発いただく予定になっています。
あとは、通訳の問題ですね。通訳する人に現場の知識がない状態だと、全く違う意味に伝わってしまうということがあります。現場で目を合わせながら、身振り手振りを交えて伝えるのとではやはり大きな差があります。
梅田
逆にリモート教育を行うことで見えてきた良かった点はありますか?
太田様
渡航費用、滞在費用などはかなり浮くようになりました。その分教育する期間を伸ばすことも可能になりました。国内のようにゆっくりじっくり時間をかけて教育することが可能になったんです。これまでは現地に赴いたり、団体で日本に来たりする場合スケジュールの調整が大変でしたが、リモートであれば日程調整も簡単です。また講師も、移動が伴わないため、より多くの現場を受け持つことができるようになりました。
教育だけではなく幹部による進捗管理ミーティングなども、SynQ Remote(シンクリモート)を使うことで円滑に行うことができそうですし、突発的な災害や機械トラブルに対してもリアルタイムの対応ができると感じています。
梅田
これからは現地教育とリモート教育のいいとこどりをして、ハイブリッドな教育システムを構築していかれるのですね。
SaaSを活用した非同期での海外工場の遠隔管理/教育について
梅田
一緒に今回のセミナーを開催した東京ファクトリー「Proceedクラウド」のご紹介です。
創業者の池実さんは川崎重工業株式会社でボイラの生産技術に従事。BCGにて製造業を中心としたDX事業に従事したのち、2020年4月に株式会社東京ファクトリーを創業し、「Proceedクラウド」の開発をスタートされました。
池様
SynQ Remote(シンクリモート)は同期コミュニケーションを中心としたサービスですが、弊社は非同期での海外工場の遠隔管理/教育に有効な「Proceedクラウド」を開発・販売しております。
コロナ禍が長期化した影響で、サプライチェーン管理の難易度は上昇しています。私も川崎重工業時代は海外の工場を管理していましたが、日本で設計したものを海外で作る場合、従来はスーパーバイザーなど技術のある人が海外に一定期間出張して現地を確認していました。しかし現在ではクイックに海外に行くことも難しい状況です。
また、現場が同時に抱える課題として生産現場の情報が分散しているということが挙げられます。日報や、現場の掲示板、工数集計システム、メールやPCのローカルなど情報が様々な場所に分散しているため、振り返りや情報共有が難しいのです。
我々の「Proceedクラウド」は工程写真をベースに、製造情報のデータベースを構築することによってサプライチェーン、すなわち外注先の可視化を実現するものです。
詳しい機能は製品ページをご覧ください。
従来製造現場には、デジカメで撮影し、煩雑な整理を経てローカルに保存される膨大な写真がありました。「Proceedクラウド」を使えば、スマホで撮影するだけで位置情報を元に整理と共有までが即座に行われます。まずはそこで大幅な業務効率化が可能になりますが、それだけではなく、生産情報データベースが構築されることによって技能継承まで可能になり、QCD(Quality、Cost、Delivery)の改善に長期的に貢献できるツールになっています。
実際にプラントエンジニアリング会社ではインドや韓国などのサプライヤーの監視に活用いただいています。日本から調達担当の方が、いつでも「Proceedクラウド」にアクセスすることで進捗を把握でき、手配漏れなどのリスクも軽減できています。
また、日本の町工場でも活用いただいています。手順書やマニュアルなどが整理されておらず、ノウハウが暗黙知になっていたところ、「Proceedクラウド」によってベテランの作業を記録し作業の標準化が行えるようになったとのお声をいただいています。
梅田
まさに町工場での利用は「教育」に活用されていますね。いすゞテクノのお二方も今日は貴重なお話をありがとうございました!